Was written for MBA 507, Ethics in Managements class at Stony Brook University on July 03, 2020
"There have been COVID-19 outbreaks at several meat processing plants across the country since March when the virus was first characterized as a pandemic," reported Tyko of USA TODAY. "In late April, President Donald Trump signed an executive order aimed at keeping the facilities open."
In March 2020, a health emergency hit the world and forced many businesses to fall under "non-essential" classification and close down. However, the food and meat processing company Tyson Foods (Tyson) fell under the "essential" businesses category and maintained a full workforce. While staying open, at least 4,500 employees got sick, and 18 died due to COVID-19 (Taylor, 2020).
The ethical dilemma remains: what is more important, the safety and health of Tyson employees, or the essential food supply of the entire nation?

In this paper, I will discuss my opinion regarding the ethical issue of which stands when keeping the Tyson factory open. Furthermore, I will discuss the background of the Tyson company, how it sacrifices the health and safety of its workers during the pandemic, what it could have done to satisfy its responsibility to the entire nation as an essential business while keeping its employees safe, and finally my opinion on whether I support the same decision if the issue were to arise again.
Who is Tyson Foods?
Tyson was established in 1935 in Springdale, Arkansas, United States. When the company was first established, it focused on chicken distribution. Today, it operates in four segments: chicken, beef, pork, and prepared foods, (Companies History, 2020). In 2019, Tyson held 28.9% of multi-outlet sales of poultry in the United States (Kamp, 2019).
In the past few years, Tyson has been involved with a few scandals, including being reported for negative market conditions and product recalls (Kamp, 2019). In 2019 alone, Tyson recalled its chicken patties and fritters "over possible plastics and mechanical seals contamination" (Kamp, 2019). Also, the 2019 third-quarter report showed a 1.9% decline in market share due to challenging market conditions and increased operating costs. With all that being said, one would wonder if the 2020 COVID scandal shocked anyone. Nevertheless, the social responsibility of the company is in the foreground of this paper and argument.
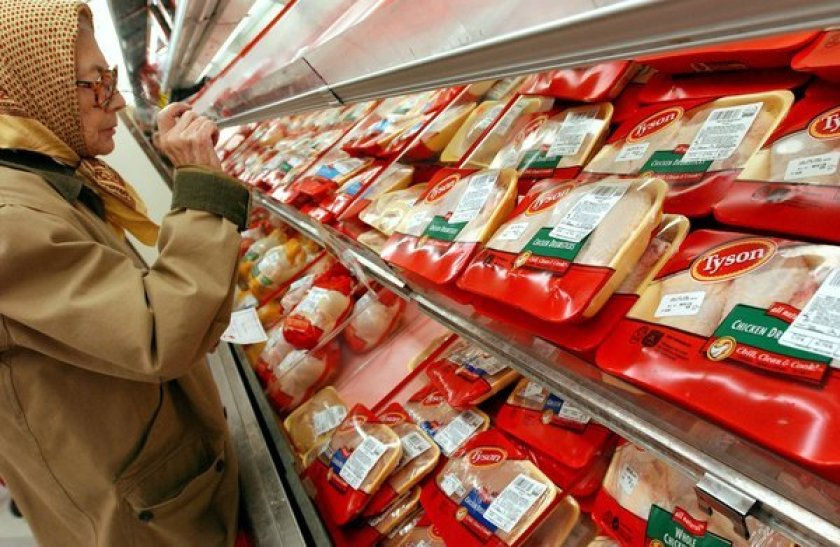
Company's responsibility
As the largest market shareholder of the food supply chain in the U.S., it is clear the company's responsibility to the public is to supply its products to consumers that rely on Tyson's operations as an instrumental need. If Tyson were to stop its operations, the public would see a drastic shortage of food. This responsibility is even heavier in times of a pandemic when most were sheltered in place. On the other hand, the company is also responsible to keep its employees (Tyson calls them Team Members) safe and healthy. Additionally, Tyson must provide safe work conditions that are not risking Team Members' health.
How did Tyson sacrifice the health and safety of its workers during the pandemic?
According to Fox Television Station, "Tyson Foods announced the results of coronavirus testing at its facilities in Benton and Washington Counties, Arkansas, and said that about 95% of employees who ultimately tested positive for the virus didn't show any symptoms" (Fox Television Station, 2020). Of the 3,748 employees tested, 481 tested positive for COVID-19, with 455 of those cases being asymptomatic (Fox Television Station, 2020).
In turn, Tyson Workers said that the factory is failing to keep them safe, (Taylor, 2020). Employees work in proximity to one another and do not offer paid sick leave. The company increased short-term disability by 90% since April 2020 to "encourage sick team members to stay home when they are sick," but it is only covering 60% of wages, and only if they are hospitalized (Taylor, 2020). This reduced pay discourages workers from taking sick leave, even if they are a risk of spreading the illness to others.
After significant public backlash, Business Insider reported that Tyson "has highlighted the new steps it's taking to protect workers, including taking temperatures, requiring face masks, instituting additional daily deep cleanings, and installing workstation dividers" (Business Insider 2020). However the COVID-19 case numbers are still spiking within the Tyson food processing plants.

What could Tyson have done to satisfy both its responsibility to the entire nation as essential business, and keep its employees safe?
When a company does not provide adequate coverage for sick leave - it demotivates workers from staying at home when they are sick. Most employees that work at the Tyson factory are low-income families that heavily rely on their jobs to survive, often working paycheck to paycheck for their families. Employees with such a socioeconomic profile are more likely to compromise their wellbeing for the sake of bringing money to the family table, especially in hard economic times. However, in this situation specifically, lives are at risk when considering a widespread disease that spreads quickly, leaving the chance of infecting everyone else in the factory. Low-income workers are seemingly more willing to risk their lives to the alternative: losing their job and their livelihood.
In a perfect world, Tyson could have satisfied both responsibilities by providing safe working conditions. Allowing safe 6 feet social distancing, requiring full face masks and body covering, providing free COVID-19 testing to all workers on a consistent basis, not allowing sick workers to enter the factory, and providing 100% paid sick-leave to those who got infected while working. By providing these safety measures, Tyson would better encourage a safe working environment for its Team Members.
Alternative 1 - Keeping the factory closed
Keeping the factory closed affects primarily the employees from the low-income families that rely on the income. Then, it affects people around the country that rely on the food supply. After all, almost 29% of the food supply is satisfied by Tyson. Furthermore, it affects the stakeholders that will lose significantly from the closing of the factory. Lastly, the factory as a whole might not survive a temporary closing and might close permanently. This emphasizes the ethical problem at hand and its complications. With that being said, closing the factory will not be optimal to both the company and society. Hence, I would not recommend this option.
Alternative 2- Compromise keeping the factory open, but reduce the capacity and provide adequate safety measures
Tyson will need to allow proper protective equipment including N95 masks and full protective bodysuits, given that proper social distancing is likely not possible. Additionally, Tyson should provide plexiglass dividers between the workers, and operate the factory at 60% capacity while alternating between the workers to increase social distancing. Workers should remain on the payroll even if at home on rotation. Over the next several months, the capacity should slowly increase as domestic health conditions permit.
Summary
In general, I believe Tyson put their workers at great risk, and better protection should have been provided early on in the pandemic. Going forward, I believe the employees' protection should be the number one priority of the company. When Tyson sacrifices the safety of its workers, negative publicly ensues, resulting in a loss of sales either way. Therefore, it is in Tyson's best interest to take these safety measures, not only for the workers but also to improve the brand image to consumers.
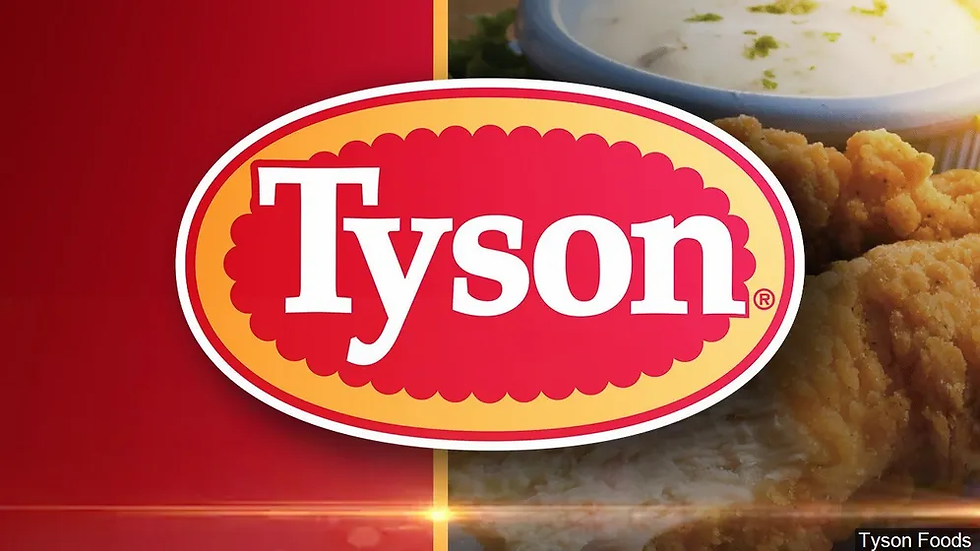
References
Alcorn, C. (2020). Tyson meat plant employee dies of Covid-19 weeks after major outbreak. Retrieved 3 July 2020, from https://edition.cnn.com/2020/05/26/business/tyson-waterloo-plant-death/index.html
Kamp, K. (2019). Poultry - US - December 2019. Retrieved 3 July 2020, from https://reports-mintel-com.proxy.library.stonybrook.edu/display/920132/?fromSearch=%3Ffreetext%3Dtyson#
Keegan, H. (2020). Tyson Foods says 371 additional workers have tested positive for COVID-19 at Missouri chicken plant. Retrieved 3 July 2020, from https://www.usatoday.com/story/money/food/2020/06/27/coronavirus-tyson-foods-noel-missouri-chicken-plant-covid-19-positive/3270136001/
Taylor, K. (2020). At least 4,500 Tyson workers have caught COVID-19, with 18 deaths. The meat giant still doesn't offer paid sick leave, as the industry blames workers for outbreaks. Retrieved 3 July 2020, from https://www.businessinsider.com/tyson-4500-covid-19-cases-as-meat-industry-blames-workers-2020-5
Tyson Foods. (2020). Retrieved 3 July 2020, from https://www.companieshistory.com/tyson-foods/
Who We Are. (2020). Retrieved 3 July 2020, from https://www.tysonfoods.com/who-we-are
Comments